EK-General – Section A ( Auxiliary Machine) Questions & Answers
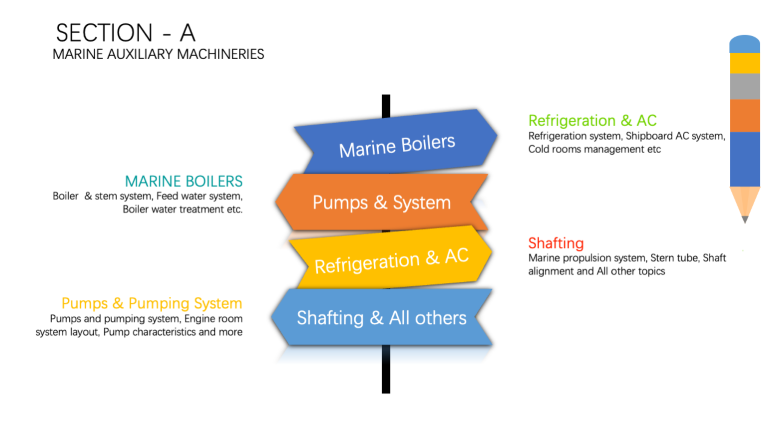
Q1. With reference to ships air conditioning plants: (a) state the temperatures and relative humidities at EACH of the points that are regarded as the boundaries of the comfort zone; (4) (b) explain how the temperatures and relative humidities could be maintained within the comfort zone when the ship is in EACH of the following locations: (i) North West Europe in winter; (3) (ii) Arabian Gulf in summer. (3) 2019/MAR/Q7 Q2. During bunkering operations, a section of deck bunker line starts leaking fuel oil from a pinhole at the mid-section of the pipe. (a) As Chief Engineer Officer, state the immediate actions to be taken to avoid a potential pollution incident; (4) (b) Explain how a permanent repair could be made, stating any precautions to be taken and any further inspections that would be required. (6) 2019/DEC/Q8 2020/OCT/Q6 Q1. Describe the principle of operation of a biological sewage treatment plant. (4) (b) Explain how anaerobic conditions can occur within a sewage treatment plant, stating the hazards that may be encountered. (4) (C) Explain the meaning and significance of the term biological oxygen demand (2) 2020/OCT/Q5 Q2. (a) Describe the operation of a vacuum sewage system. (5) (b) List the advantages of a vacuum sewage system when compared to a conventional flushing system.(4) (c) State why untreated sewage should not be allowed to stagnate. (1) 2019/MAR/Q5 Q3. Describe, with the aid of a sketch, a Membrane Bioreactor type sewage treatment plant. (10) 2017/OCT/4 Q1. With reference to air receivers: (a) explain why air receivers are prone to corrosion; (3) (b) state how corrosion can be prevented; (3) (c) if significant corrosion is detected during a regular inspection explain how the air receiver may still be safely used in service until a permanent repair can be effected. (4) 2018/JUL/Q7 Q1. Discuss the advantages and disadvantages of electrical remote monitoring and control systems compared to pneumatic systems. (10) 2016/OCT 2017/JUL/2 2020/DEC/3 Q2. (a) Sketch an annotated block diagram of a closed-loop control circuit. (5) (b) Describe how the control loop sketched in Q(a) operates. (5) 2021/MAR/Q3 Q3. (A) Explain EACH of the following control terms (i) Proportional action (2) (ii) Integral action (2) (B) Describe, with the aid of a sketch, a control system that may be enhanced by the inclusion of a cascade control. (6) 2020/OCT/Q3 Q4. With reference to automatic control systems: (a) explain the term proportional band width; (2) (b) state how the proportional band may be adjusted on EACH of the following: (i) motion balance controllers (2) (ii) force balance controllers. (2) (c) explain the consequences if the proportional band is set incorrectly. (4) 2019/JUL/Q2 Q5. (a) Explain EACH of the following control terms: (i) cascade; (2) (ii) split range. (2) (b) Describe, with the aid of a sketch, a control system that may be enhanced by the inclusion of cascade control. (6) 2013/DEC 2016/APR 2018/MAR/Q2 Q6. With reference to pneumatic instrument and control systems: (a) sketch a control air dryer as fitted downstream from the instrument air compressor or reducing valve;(6) (b) explain the operation of the dryer sketched in part (a). (4) 2017/DEC/6 Q7. With reference to pneumatically operated control valves: (a) state the reason for fitting valve positioners; (4) (b) with the aid of a sketch, explain valve hysteresis and how it affects the process; (4) (c) describe how the design and routine maintenance can limit hysteresis. (2) 2015/OCT 2017/OCT/2 Q1. With reference to deck machinery: (a) sketch a line diagram showing the layout and components of a hydraulic system with a variable delivery, pressure compensated pump and accumulator, suitable for the operation of deck machinery (5) (b) explain the advantages of using electrically driven machinery over hydraulically driven winches and windlasses. (5) 2013/JUL/7 2017/OCT/7 2018/DEC/7 Q1. (a) State the factors in the storage of welding electrodes which will assist in producing good quality welds. (2) (b) Explain the importance of edge preparation before welding. (2) (c) Sketch TWO methods of plate edge preparation. (2) (d) A hairline crack is detected in a pipe, as Chief Engineer Officer, state the factors to be taken into account in reaching a decision on the method of repair. (4) 2017/MAR/Q1 2018/JUL/Q1 Q2. As Chief Engineer Officer, prepare standing orders for working with gas cutting and gas welding equipment, including the storage of spare bottles. (10) 2015/DEC 2018/OCT/Q7 Q1. With reference to fixed installations for machinery space fires: (a) sketch a CO2 bottled system; (5) (b) explain how the system sketched in part (a) is protected from overpressure; (2) (c) describe the periodic maintenance required. (3) 2017/DEC/8 2021/MAR/Q8 Q2. With reference to fixed machinery space firefighting system which use water in the form of fog or mist, explain EACH of the following. (a) How the fire is contained and extinguished (4) (b) The importance of particle size and flow rate (4) (c) The routine testing to be carried (2) 2020/OCT/Q8 Q3. As chief engineer officer appointed to a newly acquired vessel, describe the inspection that should be carried out to ensure satisfactory condition and operation of the ship’s firefighting equipment. (10) 2020/JUL Q4. Accidents have occurred due to premature or accidental release of CO2 into the machinery spaces. (a) State the safety procedures that the Chief Engineer Officer should adopt with respect to maintenance being carried out on the system by shore contractors. (3) (b) Explain why the Chief Engineer and ships staff should still have to check on work carried out by shore contractors. (2) (c) State how the liquid levels in the CO2 bottles may be checked in situ and how often this test should be carried out. (2) (d) Explain why ship’s general service air should not be used for blowing through and testing CO2 operating lines and suggest a suitable alternative. (3) 2019/OCT/Q8 Q5. With reference to CO2 gas provided for firefighting purposes: (a) describe, with the aid of a sketch, a system for the detection and extinguishment of hold fires;(7) (b) state how the amount of gas to be released into the hold space is estimated. (3) 2019/JUL/8 Q6. With reference to fixed CO2 smothering systems for ships machinery spaces: (a) State the safety procedure that the Chief Engineer Officer should adopt with respect to maintenance being carried out on the system by contractors whilst the vessel is in port. (3) (b) State the procedure prior to the safe release of CO2 into the machinery space in the event of a fire. (4) (c) Describe the factors that should be considered prior to re-entry of the machinery spaces after the release of CO2 gas. (3) 2019/MAR/Q8 Q7. As Chief Engineer Officer, describe the examinations that were carried out during a safety equipment survey with regard to fire safety. (10) 2018/DEC/Q8 Q8. With reference to freshwater HI-FOG firefighting systems: (a) sketch such a system; (6) (b) state how the system in (a) is activated; (2) (c) state, with a reason, a suitable location for the above system. (2) 2015/OCT 2018/OCT/Q8 Q9. With reference to automatic sprinkler systems for firefighting purposes: (a) explain, with the aid of a heat release versus time diagram, the difference between fire control and fire suppression (6) (b) state the limitations of using glass bulbs to activate sprinkler heads and suggest, with reasons, an alternative mechanism. (4) 2013/JULY 2017/MAR/7 2018/MAR/Q7 Q10. The company, with which you are employed, requests that all Chief Engineer Officers prepare standing orders regarding the prevention and detection of fires in the machinery spaces. Compile such a list of recommendations to be submitted to central office. (10) 2015/MAR 2016/APR 2016/DEC 2017/JUL/8 Q1. With reference to plate heat exchangers, explain how EACH of the following design aspects promote heat transfer: (a) material selection;(5) (b) flow pattern; (3) (c) extended surface area. (2) 2013/MAR 2017/OCT/Q1 2018/JUL/Q3 2021/MAR/Q6 Q2. Discuss the factors that lead to the selection of materials for use in a sea water cooled, multi-tubular heat exchanger. (10) 2020/JUL/Q1 Q3. (a) State THREE modes of heat transfer. (1) (b)Describe how the design requirements of EACH of the following are met, detailing the materials used to promote or retard heat transfer: (i) plate cooler in central cooling system;(3) (ii) meat room in domestic provisions space;(3) (iii) auxiliary steam system pipelines. (3) 2017/MAR/Q8 DEC/2019/Q1 Q4. With reference to multi-tubular heat exchangers, explain how EACH of the following contribute to satisfactory performance: (a) tube wall thickness;(2) (b) dense population of tubes in the tube plate;(2) (c) tube materials selection;(2) (d) coolant flow rates;(2) (e) unimpeded passage of coolant at entry and exit from the tubes. (2) 2014/APR 2019/DEC/Q5 Q5. With reference to the design, construction and materials used in the manufacture of plate type heat exchangers, explain why, in most cases, they are superior to tubular type heat exchangers. (10) 2013/JULY 2019/JULY/Q5 Q6. Describe the principle of operation of EACH of the following heat exchanger types, stating a suitable application for EACH type: (a) parallel flow; (3) (b) contra flow; (3) (c) mixed flow. (4) 2015/DEC 2018/OCT/Q4 Q1. (a) State, with reasons, the control actions that may be suitable for EACH of the following processes: (i) settling tank oil temperature; (2) (ii) jacket water temperature; (2) (iii) temperature of oil being purified. (2) (b) Sketch a block diagram of ONE of the control circuits for ONE of the processes in part (a).(4) 2019/MAR/Q2 Q2. (a) Describe, with the aid of a sketch, a temperature measuring instrument that uses the principle of operation of a change in resistance with the application of heat. (6) (b) Describe how the instrument sketched in part (a) is tested and calibrated. (4) 2018/DEC/Q2 2020/DEC/Q2 Q3. Describe, with the aid of a sketch, the principle of operation of a capacitance electrode level measuring transmitter. (10) 2013/MAR 2015/DEC 2017/MAR/Q5 2020/JUL/Q2 Q4. (a) Describe, with the aid of a sketch, an explosimeter for the detection of combustible gas. (6) (b) Describe how the instrument sketched in part (a) is tested and calibrated. (4) 2018/OCT/Q2 Q1. (a) The international management code for the safe operation of ships and for pollution prevention, is commonly referred to as the ISM code. (A) Explain the objectives of ism and how are they achieved. (5) (b) List five emergency scenarios for which contingency plans may be developed under ism with respect to the engine room (5) 2017/DEC/7 2020/DEC/01 Q1. (a) State the possible causes for EACH of the following auxiliary diesel engine lubricating oil sample results (i) High acidity (2) (ii) High sediment content (2) (iii) Excessive water content (2) (iv) Fuel dilution (2) (b) explain which of the results in Q7(a) would give greatest concern (2) 2020/DEC/7 Q2. With reference to fuel oil viscosity: (a) explain why correct fuel oil viscosity is necessary; (2) (b) describe TWO methods for the measurement of viscosity that are suitable for the inclusion into a pneumatic or electronic control system: (6) (c) state, with reasons, a control action for a viscosity controller. (2) 2013/JULY 2013/DEC 2019/OCT/Q2 Q3. With reference to micro bacterial infestation: (a) list the engine room systems that may be affected by this type of contamination; (2) (b) describe the conditions required for bacteria to evolve; (6) (c) describe how the presence of microbial contamination could be detected. (2) 2018/DEC/Q3 Q4. With reference to fuel with high pour point: (a) describe test that may be carried out;(4) (b) state the measure to be taken to enable the ship to use the fuel.(6) 2017/MAR/Q4 Q1. Describe EACH of the following properties of materials: (a) strength; (2) (b) hardness; (2) (c) ductility; (2) (d) toughness (2) (e) brittleness. (2) 2021/MAR/Q1 Q2. With reference to steels used in shipbuilding and marine engineering: (a) describe EACH of the following types of failure; (i) brittle failure; (2) (ii) ductile failure. (2) (b) Explain the term ductile to brittle transition stating the factor that determines ductile to brittle transition. (2) (c) Describe a test to determine the value of brittle fracture of a specimen test piece. (4) 2018/OCT/Q1 2020/DEC/Q1 Q3. (a) Sketch a Stress/Strain curve for a mild steel test specimen. (2) (b) With reference to the curve sketched in part (a), explain EACH of the following: (i) modulus of elasticity; (2) (ii) percentage elongation; (2) (iii) ultimate tensile stress; (2) (iv) yield stress. (2) 2019/MAR/Q1 2020/OCT/Q1 Q4. Explain EACH of the following metallurgical process (a) Induction hardening (3) (b) Nitriding (3) (c) Case hardening (4) 2020/OCT/Q2 Q5. (a) Describe the properties of EACH of the following alloys used in marine engineering, giving a practical example for which, EACH are suited: (i) cupro-nickel; (2) (ii) white metal; (2) (iii) titanium. (2) (b) Discuss the merits of EACH of the following alloys for use in the casting of large propellers: (i) nickel aluminium bronze; (2) (ii) stainless steel. (2) 2019/OCT/Q1 Q6. (a) Describe, with the aid of sketches, how the test pieces for a Class 1 pressure vessel are obtained. (6) (b) List the tests which are carried out on the test pieces described in part (a). (4) 2014/DCE 2016/DEC 2019/JUL/Q1 Q7. Explain the effects of the addition of EACH of the following alloying elements to improve the characteristics of steels: (a) chromium; (2)????(b) manganese; (2)????(c) molybdenum; (2) (d) nickel; (2)????(e) vanadium. (2) 2018/DEC/Q1 Q8. With reference to machinery parts under cyclic loading, describe, with the aid of sketches, how the propagation of even the smallest of cracks can lead to total component failure. (10) 2013/OCT 2016/JULY 2018/MAR/Q1 Q9. Describe, with the aid of a graph, EACH of the following types of ferrous material failure, stating ONE practical example of EACH: 1. creep; (5)??????2. fatigue. (5) 2014/JULY 2016/OCT 2017/DEC/1 Q10. (a) Describe, with the aid of a Strain versus Time diagram, how a creep test is carried out to determine the strain rate of the material under test. (6) (b) Explain EACH of the stages sketched in the diagram in part (a). (4) 2021/MAR/Q2 Q1. (a) Discuss the merits of a condition monitoring system compared to other maintenance regimes. (5) (b) Describe how the data is gathered, stored and evaluated on a computer-based vibration analysis system. (5) 2016/OCT 2017/JUL/1 Q2. Following bunkering operations, it is discovered that the vessel received a quantity which was short of what was stipulated in the pre-delivery document. As Chief Engineer Officer, write a Note of Protest to the Master of the bunkering vessel. (10) 2018/MAR/Q8 Q3. Explain the legal, administrative and technical responsibilities of a Chief Engineer Officer.(10) 2017/OCT/8 2019/JUL/7 Q4. State the inspections, instructions and maintenance that should be carried out on main sea water pipelines, strainers and ship’s side valves to minimise the risks of engine room flooding. (10) 2013/DEC 2016/APR 2018/JUL/Q4 Q5. (a) Sketch an engine room fresh water central cooling system, indicating the water temperatures at salient points on the system. (6) (b) State, with reasons, FOUR advantages of the system sketched in part (a) compared to one which is totally sea water cooled. (4) 2017/JUL/3 Q6. With reference to medium speed auxiliary diesel engines: (a) explain why twin air inlet and exhaust valves are often fitted to each cylinder head; (6) (b) explain why, in some cases, valve rotation is employed. (4) 2017/JUL/7 Q1. With reference to centrifugal separators used for oily bilge duty: (a) explain why centrifugal oily water separators are superior to those which rely on gravity (3) (b) describe, with the aid of a sketch, how flow over the centrifugal separator plates can break down emulsions by encouraging flocculation of particles and coalescence of droplets; (5) (c) state how the bilge overboard control valve can only operate by the Chief Engineer:(1) (d) state a value of overboard parts per million oil content that may be set which is below the generally recommended value. (1) 2021/MAR/Q5 Q2. (a) Sketch an oily water separator that compiles with current MARPOL regulations. (b) Describe a monitoring system that ensures that the oil discharge content is below the recommended maximum and that logs and retains data. Also mention any other measures to ensure that illegal discharges are prohibited. 2020/DEC/6 Q3. Describe, with the aid of a sketch, the principle of operation of a static oily water separator that utilises a separating matrix and polishing pack. (10) 2019/OCT/Q4 Q4. Describe in detail the operation, maintenance and monitoring of a bilge water processing unit to ensure compliance with the current MARPOL convention on the discharge of oily bilge water.(10) 2019/MAR/Q4 Q5. With reference to static oily water separators, explain EACH of the following: (a) why the supply pump should be carefully selected and matched to the separator; (2) (b) how the separator achieves effective separation; (4) (c) how the physical properties of each of the fluids to be separated affects the rate and effectiveness of separation. (4) 2013/OCT 2015/DEC 2017/MAR/3 Q1. With reference to podded thrusters for main propulsion: (a) distinguish between podded and azimuthing thrusters; (4) (b) explain the meaning of thruster and tractor propellers, stating ONE advantage of tractor units; (4) (c) explain what is meant by tandem podded thrusters. (2) 2019/MAR/Q3 Q2. With reference to vessels fitted with podded propulsion systems capable of being rotated through 360°: (a) state the advantages claimed over conventional shafting and steering arrangements; (6) (b) state, with reasons, the type of vessels that are most suited to this means of propulsion. (4) 2017/OCT/3 2020/OCT/Q4 Q3. (a) Define propeller slip, explaining how it is calculated. (2) (b) State, with reasons, FOUR conditions which will affect the propeller slip. (8) 2014/APR 2017/DEC/Q2 2021/MAR/Q4 Q4. With reference to propeller cavitation; (a) define cavitation (2) (b) describe FOUR detrimental effects of propeller cavitation (8) 2020/JUL Q5. With reference to a keyless propeller designed for hydraulic (wet) fit and withdrawal: (a) describe, with the aid of a sketch, how the propeller is fitted to the tail shaft; (6) (b) state TWO advantages compared to a dry fit; (2) (c) explain how the thrust is transmitted without the use of a key and keyway. (2) 2019/JUL/Q3 Q6. With reference to large fixed bladed propellers: (a) describe, with the aid of a sketch, EACH of the following: (i) the effect of hull fouling; (3) (ii) operation in clean hull, ballast condition. (3) (b) explain why fitting a light propeller may be beneficial. (4) 2015/OCT 2019/JUL/12 Q1. With reference to centrifugal pumps; (a) Sketch double entry impeller showing directions of flow (3) (b) Explain why double entry impellers are fitted (2) (c) Explain, with the aid of a head versus flow diagram, why a two-speed pump is preferable to throttling where high and low capacities are demanded for a large sea water circulating pump. (5) 2020/DEC/5 Q2. With reference to pump selection, state any TWO types of pump for EACH of the following applications, stating why they are suitable. (a) bilge pumping (2) (b) Cargo oil stripping (2) (c) Sewage sludge (2) (d) Lubricating oil circulating (2) (e) Sea water circulating (2) 2020/JUL Q3. (a) Describe TWO systems of priming centrifugal pumps. (6) (b) List the advantages of EACH of the priming methods described in part (a). (4) 2017/OCT/5 2019/DEC/Q4 Q4. With reference to centrifugal pumps: (a) explain the operating principle of a centrifugal pump and state why it is unnecessary to fit a relief valve to it; (3) (b) explain why some pumps have a double entry impeller; (2) (c) describe a routine overhaul of a centrifugal pump, stating the inspections, measurements and possible replacement parts that may be required. (5) 2019/OCT/Q5 Q5. With reference to centrifugal pumps: (a) Explain how the performance may be assessed without the need to dismantle the pump; (3) (b) state the effects of misalignment between the driving motor and the pump; (3) (c) describe, with the aid of a sketch, how on a new replacement motor, alignment is checked and adjusted. (4) 2019/JUL/Q4 Q6. (a) Describe, with the aid of a sketch, a constant speed, uni-directional, axial flow pump suitable for hydraulic applications. (6) (b) Explain, with the aid of a sketch, how the axial flow pump can achieve higher pressures than its radial flow counterpart. (4) 2019/MAR/Q6 Q7. With reference to centrifugal pumps: (a) state the operating principle of a centrifugal pump and why it is unnecessary to fit a relief valve to it;(2) (b) State TWO impeller types, explaining which type of application EACH would be best suited for; (4) (c) Explain why cavitation occurs, and how it is reduced by design (4) 2015/MAR 2016/APR 2017/DEC/4 2018/OCT/Q5 Q8. (a) State the affinity laws for a centrifugal pump. (3) (b) State the effects on the pump affinity laws of fitting a slightly smaller diameter impeller. (2) (c) Explain, with the aid of a Head versus Flow diagram, why a two-speed pump is preferable to throttling where high and low capacities are demanded for a large sea water circulating pump. (5) 2013/JULY 2014/OCT 2018/MAR/Q4 Q9. With reference to centrifugal pumps and pumping systems: (a) explain, with the aid of a diagram, the distinction between Net Positive Suction Head available (NPSHa) and Net Positive Suction Head required (NPSHr); (8) (b) explain how the NPSHa may be increased by design. (2) 2017/JUL/Q4 Q1. With reference to ships air conditioning plant: (a) Define the term comfort zone (2) (b) State the objectives of maintaining the conditioned air within the comfort zone (3) (c) State, with reasons, FIVE areas from which the conditioned air must not be recirculated. (5) 2020/OCT/Q6 Q2. (a) State a block diagram of a fully automated air conditioning system for accommodation spaces, annotating the relevant temperatures and relative humidities throughout the system. (7) (b) Describe how bacteria are prevented from multiplying to a harmful level in an air conditioning system. (3) 2020/JUL/Q7 Q3. (a) Sketch a diagrammatic arrangement of a fully automatic direct expansion domestic refrigeration system which supplies a number of cold rooms. (5) (b) State, with reasons, FIVE desirable thermodynamic properties of a refrigerant. (5) 2016/JULY 2018/MAR/Q6 2019/DEC/Q6 Q4. With reference to the lubrication of refrigeration compressors: (a) state the advantage of using fully synthetic oils; (2) (b) explain why oil may be carried over from the compressor; (3) (c) describe a device which returns oil from the compressor discharge to the compressor sump; (3) (d) state TWO reasons why an accumulation of oil in the evaporator is undesirable. (2) 2013/DEC 2015/OCT 2019/OCT/Q6 Q5. With reference to a vapour compression refrigeration plant: (a) explain the purpose of EACH of the following: (i) expansion valve; (2) (ii) room thermostat; (2) (iii) high pressure cut out. (2) (b) explain why EACH of the following conditions are desirable: (i) superheating at the compressor suction; (2) (ii) undercooling at the condenser outlet. (2) 2018/DEC/Q6 Q6. With reference to refrigeration systems: (a) explain why undercooling of the refrigerant at the condenser outlet is desirable; (3) (b) describe, with the aid of a sketch, how a heat exchanger could be incorporated in the circuit to enhance undercooling; (5) (c) explain the possible consequences of the refrigerant having a dryness fraction at the compressor suction. (2) 2014/APR 2014/JULY 2016/OCT 2018/JUL/Q6 Q7. With reference to a domestic refrigeration plant, state TWO causes of EACH of the following conditions, stating how EACH cause may be rectified: (a) excessive pressure; (2) (b) low pressure at evaporator suction; (2) (c) compressor cycling; (2) (d) compressor running for long periods but not lowering the temperature in the cold rooms. (2) (e) compressor operating noisily. (2) 2017/JUL/6 Q8. With reference to ships’ air conditioning systems: (a) state the effects of EACH of the following faults: (i) corroded return air trunkings; (2) (ii) blocked evaporator drains; (2) (iii) defective capacity control. (2) (b) state the main health hazard that may arise in the air conditioning plant, stating the conditions that need to arise and the measures that should be taken to prevent this occurring. (4) 2013/MAR 2017/MAR/Q4 Q1. Following a serious machinery space fire, the engine room was abandoned, and an inert gas smothering agent used to extinguish the fire. Write a report to the Superintendent Engineer detailing the sequence of events which led to this course of action and the subsequent actions taken to enable the vessel to proceed on passage. Include conclusions and recommendations in the report. (10) 2016/JULY 2019/DEC/Q7 Q2. As Chief Engineer Officer on board a vessel which has lost 50 litres of lubricating oil from the stern tube system to sea overnight, write a report to the Superintendent Engineer outlining the actions taken to rectify the leakage and any other further recommendations. (10) 2016/APR/Q7 2018/JUL/Q2 Q1. With reference to main thrust block arrangements (a) Explain how the tilting pads assist in the formation of an oil wedge (2) (b) Describe the actions that may be taken if upon inspection the pads are found to be ??(i) Lightly scored (2) ??(ii) Wiped (2) (c) Explain how the thrust clearance may be measured, stating a typical value (2) (d) State the possible effects if the thrust clearance is incorrect (2) 2020/DEC/4 Q2. (a) Describe, with the aid of a sketch, the principle of operation of a modern shaft torsion meter. (8) (b) Explain why it is important in terms of hull efficiency to measure and compare shaft torque and speed. (2) DEC/2019/Q2 Q3. Describe, with the aid of a sketch, the principle of operation of a radial lip stern tube sealing arrangement for an oil filled stern tube, which incorporates an air space and is designed to prevent pollution. (10) DEC/2019/Q3 Q4. With reference to stern tube bearings: (a) explain why white metal lined bearings are susceptible to failure; (5) (b) outline the merits of non-metallic bearings. (5) 2016/APR 2019/OCT/Q3 Q5. (a) Explain how power is transmitted through main propulsion shafting. (3) (b) State THREE operational factors that may induce high stress in shaft coupling bolts. (3) (c) Sketch a hydraulic type of shaft coupling bolt. (4) 2014/JULY 2015/JULY 2015/OCT 2018/DEC/Q3 Q6. With reference to propeller shaft alignment: (a) state the objectives of a satisfactory alignment; (3) (b) state the conditions that must be met to achieve satisfactory alignment; (3) (c) explain what is meant by fair curve alignment. (4) 2018/OCT/Q3 Q7. With reference to main propulsion shaft systems: (a) describe a method of hydraulic jacking to check bearing loads; (5) (b) sketch the Bearing Load versus Shift Lift Dial Gauge Reading graph obtained by the method described in part (a), annotating the graph and how the characteristic of bearing load is obtained.(5) 2014/OCT 2018/MAR/Q3 Q8. (a) Sketch an outboard radial lip seal as fitted to an oil lubricated stem tube. (5) (b) Explain the procedure for replacing the seal sketched in part (a) without removing the tail shaft. (5) 2017/MAR/Q2 Q1. With reference to activated fin stabilisers, explain EACH of the following: (a) why such units are preferred to passive tanks in large vessels; (3) (b) why these units are preferred for passenger and fast cargo ships; (3) (c) why partial, rather than maximum damping of ship movement in heavy weather, is advisable for reasons other than overstressing the fin stocks and activating gear. (4) 2014/DEC 2018/DEC/5 Q2. With reference to tunnel type bow thrusters: (a) explain why some vessels are fitted with more than one bow thruster: (2) (b) discuss the options available in terms of prime mover and transmission systems. (8) 2013/JULY 2016/JULY 2019/OCT/Q6 Q3. Describe, with the aid of a block diagram, a compensated control system for an active fin stabilisation unit. (10) 2013/JULY 2017/JUL/5 Q1. Sketch a hydraulic circuit for a FOUR ram steering gear that allows FIVE different ram combinations to be used, identifying EACH ram and valve combination. (10) 2021/MAR/Q7 Q2. (a) Sketch the hydraulic circuit for a ram type steering gear that complies with the single failure concept and automatic isolation. (6) (b) Describe how automatic isolation, for the hydraulic circuit sketched in part (a), is achieved within 45 seconds should leakage of system oil occur. (4) 2014/JULY 2015/DEC 2018/JUL/Q5 2020/JUL Q3. The steering gear operation of a vessel that recently experienced a heavy storm is found to be abnormally sluggish. (a) State FIVE reasons for possible malfunction of the gear. (5) (b) State the corrective actions that may be carried out at sea, that will allow the vessel to continue to the nearest port. (5) 2014/OCT 2016/OCT 2019/DEC/6 Q4. (a) State the regulations pertaining to the main and auxiliary steering gear with reference to EACH of the following: (i) rudder angle and time of operation;(2) (ii) electrical supply. (3) (b) With reference to a hydraulic steering gear, explain EACH of the following: (i) the factors that may contribute to the failure of a hydraulic pipe coupling; (2) (ii) what is meant by the single failure concept. (3) 2013/OCT/5 2017/DEC/5 2018/OCT/Q6 2018/MAR/Q5 Q1. With reference to the treatment of domestic water for potable use. (a) describe the principle of operation of a steriliser that uses silver irons; (4) (b) State the advantages of silver iron sterilisation over other methods; (2) (c) State the inspections and maintenance that should be carried out on EACH of the following; (i) Fresh water tanks (2)????(ii) calorifiers (2) 2020/JUL/Q1 Q2. With reference to bacteria harmful to humans in drinking and washing water: (a) state the constraints placed on the installation and use of systems for shipboard production of fresh water; (3) (b) state the maintenance and treatment recommended for freshwater tanks; (3) (c) describe how the entire freshwater system can be made free from bacteria; (3) (d) state an acceptable residual value in the freshwater tanks to ensure the correct concentration of treatment in the system. (1) 2013/JULY 2015/JULY 2016/DEC 2017/OCT/6 2014/APRANNEX-1, OIL POLLUTION
ANNEX IV, SEWAGE TREATMENT
COMPRESSED AIR SYSTEM
CONTROL & AUTOMATION, REMOTE CONTROL, UMS
DECK MACHINERY
FABRICATION & WELDING
FIRE & SAFTY, CO2 SYSTEM
HEAT EXCHANGERS
INSTRUMENTATION & MEASUREMENT THEORY
ISM CODE
LUBE OIL, FUEL OIL
MATERIAL SCIENCE
MISCELLANEOUS
OILY WATER SEPERATOR
PROPULSION & PROPELLER THEORY
PUMPS & PUMPING SYSTEM
REFRIGERATION & AIR CONDITIONING
REPORT WRITING
SHAFTING, STERN TUBE
STABILIZER, THRUSTERS
STEERING GEAR & RUDDER
WATER PRODUCTION, WATER TREATMENT