BOILER WATER TREATMENT FUNDAMENTALS
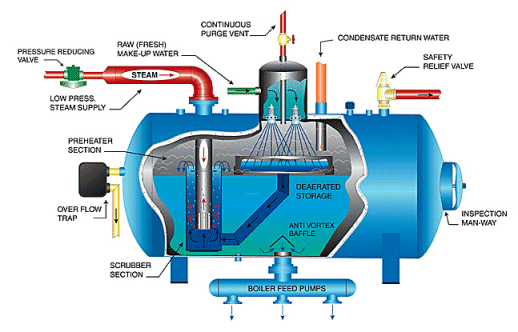
Boiler basics and types of boilers | Common issues found on Boiler feed water | Boiler water treatment fundamentals | Water Treatment Philosophy and Overview |Boiler Water Treatments and its purpose
BOILER WATER TREATMENT FUNDAMENTALS
- The concept of employing water, fresh or distilled, as a power generating source and heat exchange medium originated and was realised with the inception of the steam generator or boiler, and has been applied most successfully and beneficially in this manner ever since.
- Water has the ability to transfer heat from one surface to another, thereby maintaining the system within the correct operational temperature range while generating steam to carry out work. However, water can adversely affect metal components under the operational conditions normally found in steam boilers and other heat exchange devices.
- The extent of deterioration depends on the specific characteristics of the water and the system in which it is being used.
- In order to counteract the detrimental properties normally attributed to water and its contaminants (dissolved and suspended solids and dissolved gases), special chemical treatment programmes have been devised.
- Accepted water treatment processes and procedures are constantly being upgraded and modernized, and new methods are being developed to complement and/or replace older ones.
- Although water from marine evaporators and boiler condensate return systems is essentially “pure”, minute quantities of potentially harmful salts and minerals can be carried by this composition and feed water into the boiler, where they will accrue, ultimately resulting in serious problems in the steam generating unit. In addition, the water can also contain dissolved gases, i.e. CO2 and Oxygen, which can result in corrosion of the system.
- Using unprocessed fresh water (e.g. shore water) as a makeup source can present some of the same problems experienced with distilled water, but in addition, certain contaminants which are naturally present in fresh water can be extremely destructive in boiler systems if not dealt with promptly and effectively soluble salts such as Chloride, Sulphate and Carbonate are present.
- as electrolytes in the untreated water, leading to galvanic and other types of corrosion, depending on the conditions in the system. In addition, Sulphates and Carbonates have the potential to form insoluble, adherent, insulating “hard water” scale deposits on heat exchanger surfaces.
CONTRIBUTING ELEMENTS WHICH AFFECT BOILER WATER TREATMENT
- Most dissolved mineral impurities in water are present in the form of ions. These ions contain an electrical charge which is either positive (cation) or negative (anion). These ions can join together to form chemical compounds. To know which ions will combine, we need to know their electrical charge.
- Ions of concern to us include the following:
Positive ions | Chemical symbol | Negative ions | Chemical symbol |
Sodium Calcium Magnesium Hydrogen | Na+ Ca++ Mg++ H+ | Chloride Bicarbonate Carbonate Hydroxide | Cl– HCO3 CO3 – – OH– |
- An example of this combining of ions is the action between Calcium and Carbonate. The chemical compound which forms is Calcium Carbonate.
- Other impurities which will affect the boiler water treatment control include Copper, Iron Oxides, oil and dissolved gases.
Copper
- Copper is introduced into a system by corrosion of Copper piping and Copper alloys. In boilers, the source of this corrosion could be dissolved gases in the boiler water or the excessive use of Hydrazine which will corrode Copper and Copper alloys, allowing Copper to be carried back to the boiler.
- Copper in the boiler displaces metal from the tube surfaces and plates out on the tubes. This condition often occurs under existing scale and sludge deposits, which is known as under deposit Copper corrosion.
- Copper deposits are a serious problem in high pressure boilers. Waterside deposits may be submitted to Unitor for complete analysis and determination of the correct procedures to follow for cleaning.
Oil [1]
- To prevent oil from entering condensate and feed water systems, certain safety equipment is generally incorporated to detect, remove, and arrest such contamination.
- Oil contamination may occur through mechanical failure, for example, faulty oil deflectors at turbine glands passing lubrication oil to gland seal condensers and main condensers, etc., or undetected leaks at tank heating coils.
- Any oil film on internal heating surfaces is dangerous, drastically impairing heat transfer. Oil films therefore cause overheating of tube metal, resulting in possible tube blistering and failure.
- If oil contamination is suspected, immediate action must be undertaken for its removal. The first corrective measure in cleaning up oil leakage is to find and stop the point of oil ingress into the system. Then, by using a degreaser, a cleaning solution can be circulated throughout the boiler system to remove the existing oil contamination.
- Complete details on this cleaning operation are covered later in the handbook. Boiler Coagulant can assist in removing trace amounts of oil contamination.
Iron Oxides
- Iron may enter the boiler as a result of corrosion in the pre-boiler section or may be redeposited as a result of corrosion in the boiler or condensate system. Often, Iron Oxide will be deposited and retard heat transfer within a boiler tube, at times resulting in tube failure. This usually occurs in high heat transfer areas, i.e. screening tubes nearest to the flame.
- When iron is not present in the raw feedwater, its presence in the boiler indicates active corrosion within the boiler system itself.Rust, the reddish form, is fully oxidized. More often, in a boiler with limited Oxygen, it is in the reduced or black form as Magnetite (Fe3O4).
- Fe3O4 is magnetic and can be readily detected with a magnet. It is a passivated form of corrosion and its presence shows that proper control of the system is being maintained.
Magnesium Carbonate (MgCO3)
- Magnesium hardness in fresh water usually accounts for about one third of the total hardness. The remaining two thirds can normally be attributed to calcium.
- Since Magnesium Carbonate is appreciably more soluble in water than Calcium Carbonate, it is seldom a major component in scale deposits. This is due to the preferential precipitation of the Carbonate ion by Calcium as opposed to Magnesium which remains in solution until all soluble Calcium is exhausted.
- Once this point is reached, any free Carbonate remaining in solution will combine with the Magnesium and begin precipitating out as Magnesium Carbonate when the solubility of this salt is exceeded. Because of this latter phenomenon, where “soft” water is used for boiler structure, any Magnesium present must be removed along with the Calcium.
Magnesium Sulphate (MgSO4)
- Magnesium Sulphate is an extremely soluble salt, having a solubility of 20 % in cold water and 42 % in boiling water. It exists as the Sulphate only in water with a low pH. Because of its high solubility, it will not normally precipitate.
- The Sulphate ion, however, will be precipitated by the Calcium hardness present if no free Carbonate exists
Magnesium Chloride (MgCl2)
- Magnesium Chloride, like Magnesium Sulphate, is soluble in fresh water. In the high temperature and alkaline conditions normally maintained in a boiler, any soluble Magnesium ions in the boiler water become extremely reactive with Hydroxyl ions, which may be present in high concentrations in this type of environment.
- This can result in the formation of Magnesium Hydroxide precipitates which form insulating scale on the boiler tube surfaces. If Chloride ions are also available, they react with the Hydrogen ions previously associated with the precipitated Hydroxyl ions, to form Hydrochloric acid, thereby lowering the alkalinity of the water. If this situation is
allowed to continue, - the pH of the boiler water will decrease until acid conditions result in corrosion of the metal surfaces. Unlike Carbonate and Sulphate ions, the Chloride ion does not precipitate in the presence of soluble Calcium.
Silica (SiO2)
- Silica scale is not normally found in boiler systems except in minute quantities. It can be admitted to the system when severe carryover occurs in evaporators processing water with a high Silica content.
- Other sources of such feedwater may be high Silica river or raw fresh water as well as distilled/deionized or unprocessed fresh water which has been stored and taken from cement-washed or silicatecoated tanks.
- Once formed, pure Silica scale is extremely difficult to remove. It forms a tight adherent glass-like film on metal surfaces, thereby preventing proper heat transfer. In addition, in steam-generating devices it can carry over with the steam coating the after-boiler sections, particularly the superheater.
- If a turbine forms part of the system, the Silica can deposit on the blades as well as cause erosion of the finned surfaces of the blading, resulting in imbalance of the turbine, which in turn may result in turbine failure.
- Besides the pure form of Silica (i.e. Silicon Dioxide), possible Silicate deposits can form in combination with Calcium and Magnesium, which are extremely insoluble in water and very difficult to dissolve and remove.
- Besides being an extremely difficult process, the chemical removal of Silica and silicate deposits can also be very hazardous, since it involves the use of Hydrofluoric Acid or Ammonium Bifluoride, both of which are severely destructive to human tissue by inhalation, ingestion and physical contact. In some instances, alternate acid and alkaline
washings have been used to successfully combat this problem.The only alternative to chemical cleaning is mechanical removal.
Calcium Carbonate (CaCO3)
- Calcium Bicarbonate alkalinity exists in almost all unprocessed fresh water under normal conditions. Its solubility is about 300–400 ppm at 25 °C. If heat is applied or a sharp increase in pH occurs, the Calcium Bicarbonate breaks down to form Carbon Dioxide and Calcium Carbonate.
- While the bicarbonate salt has been shown to be moderately soluble in water, the solubility of Calcium Carbonate at 25 °C is only about 14 ppm. This value continues to decrease as the temperature increases, becoming the least where the temperature is greatest. In a boiler, this would be on the surface of the furnace tubes where contact is made with the
water. - The resulting insoluble Calcium Carbonate precipitate forms “building block-like” crystals which adhere not only to one another, but also to the hot metal surfaces, resulting in a continuous, insulating scale deposit over the entire heat exchange area.
- This deposit will continue to grow, building upon itself to form a thick coating until all the Calcium Carbonate produced is exhausted. If suspended matter is also present in the water, it can become entrained within the crystal structure, creating a larger volume of deposit than that formed by the Carbonate precipitation alone.
- If this condition is allowed to continue, heat exchange efficiency at the water/tube interface falls rapidly, resulting in an increase in fuel consumption necessary to compensate for the decline in thermal transfer and to regain design temperature as well as steam production requirements.
- This increase in the furnace-side temperature needed to run the system at optimum conditions exposes the metal surfaces to overheating which, in turn, can cause blistering fatigue, fracture, and failure of boiler tubes. In addition, if pockets of water become trapped beneath the scale deposits and are in contact with the hot metal surfaces, concentration of acid or alkaline materials may occur and lead to the formation of local electrolytic cells (under deposit corrosion).
Calcium Sulphate (CaSO4)
- Although Calcium Sulphate is more soluble in water than Calcium Carbonate, it can be just as troublesome when present in boiler and cooling water systems. Calcium Sulphate, like Calcium Carbonate, but unlike most salts, has an inverse temperature/solubility relationship in water.
- As gypsum, the hydrated form in which Calcium Sulphate is normally present in fresh water, its solubility increases until a temperature of about 40 °C is achieved. At 40 °C, its solubility is 1,551 ppm; at 100 °C, which is the normal boiling point of water, its solubility decreases to 1,246 ppm, and at 220 °C it falls to 40 ppm.
- Calcium Sulphate reacts at high-temperature surfaces essentially in the same manner as Calcium Carbonate and with the same effects and consequences. However, whereas Calcium Carbonate deposits are relatively easy to remove using a comprehensive acid cleaning procedure, Calcium Sulphate is essentially impervious to the effects of normal acid descaling methods and usually must be removed by mechanical means.
Dissolved Gases
- Gases such as Oxygen and Carbon Dioxide that are dissolved in distilled or fresh water, will further contribute to the deterioration of the boiler system. Dependent upon conditions in the system (e.g. temperature, pressure and materials of construction),
- dissolved Oxygen can cause pitting corrosion of steel surfaces, while Carbon Dioxide lowers the pH, leading to acid and galvanic corrosion. Carbon Dioxide has the added
disadvantage of forming insoluble carbonate scale deposits in an alkaline environment when Calcium and Magnesium are present.
Acidity, Neutrality and Alkalinity
- All water can be classified into one of these categories. Acidity, Neutrality and Alkalinity are only very general terms. We require more accurate methods of testing to know the degree of each condition.
- When testing boiler water, it is important to understand what you are testing for.
ALKALINITY
- The presence of Alkalinity in a water sample may be due to many different substances. For the sake of simplicity, the presence of Bicarbonate, Carbonate and Hydroxide contributes to the alkalinity of water.
P ALKALINITY.
- Phenolphtalein (P) Alkalinity (pH values greater than 8.3) measures all the Hydroxide and one half of the Carbonate Alkalinity which is sufficient for our purpose of control. Bicarbonates do not show in this test as they have a pH of less than 8.4.
M ALKALINITY.
- Total Alkalinity or M Alkalinity (pH values greater than 4.3) measures the sum of Bicarbonate, Carbonate and Hydroxide Alkalinity.
pH [2]
- The pH of a solution is a measurement of the concentration of active acid or base (alkaline constituent) in a solution. To give a precise definition, pH is the negative logarithm of the Hydrogen ion concentration.
- A simpler explanation of pH is that it is a measure of relative acidity or alkalinity of water. In other words, it reflects how acidic or alkaline the water is. pH is the number between 0 and 14 which denotes the degree of acidity or alkalinity.
- A pH value of 7 indicates neutral. Below 7 indicates increasing acidity. Above 7 up to 14 indicates increasing alkalinity.
- pH is a very important factor for determining whether a water has a corrosive or scale-forming tendency. Water with a low pH will give rise to corrosion of equipment.
.