How watertightness of watertight bulkhead maintained where bulkheads are pierced by longitudinal beams or pipes
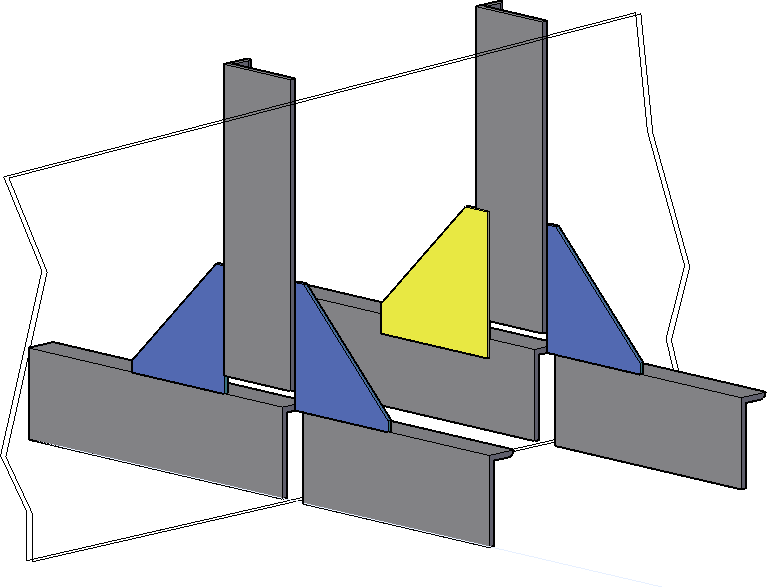
How watertightness of watertight bulkhead maintained where bulkheads are pierced by longitudinal beams or pipes.
The watertight bulkheads are provided in the ship for the following purposes;
- Strength: provide major resistance to hogging, sagging, racking, water pressure etc.
- Separation – segregates incompatible cargoes and dissimilar compartments.
- Safety (fire) – provide main vertical zones for the containment of fire, heat and smoke.
- Sub-division – divides the ship into watertight compartments to contain flooding (so that sinkage, heel or trim does not immerse the margin line.
Water tightness is maintained by fixing adequate sealing on the way of shaft in the protruding surface. There are many conventional type of sealing used, especially the older ships had an oversize hole in the bulkhead with a stuffing box fitted, fastened by studs to the bulkhead. Tightening of the bolts compresses hemp packing onto the shaft. Now the most commonly used types are of 1. Screw type gland packing, 2. Mechanical seal
1. Screw type gland packing
– Male and female halves of a gland around the cable are screwed together.
– Neoprene seal and felt washer are compressed to make a good seal.
2. Mechanical Seal
– Mechanical seal as shown in the sketch is also widely used.
– 2 identical seals are provided on the either side of the shaft for better sealing.
How the bulkheads are tested for water tightness
* Each watertight sub-division bulkhead, whether transverse or longitudinal shall be constructed in such a manner, that it shall be capable of supporting, with proper margin of resistance, the pressure due to maximum head of water, which it might have to sustain in the event of damage to ship but at least the pressure due to head of water up to margin line.
* Testing main compartments by filling them with water is not compulsory
* When testing done by filling water is not carried out, a hose test shall be carried out where practicable.
{Hose test:- 3.5 bar nozzle pressure at 1 meter distance from bulkhead}
(Hose to bulkhead distance should not be less than 1meter)
* Where hose test is not practicable because of possibility of damage to machinery. Electrical equipments etc. test may be replaced by careful visual examination of welded connection, where ever necessary by dye penetrant test / ultrasonic leak test / equivalent test.
* In any case through inspection of watertight bulkhead shall be carried out.
* Tanks which are intended to hold liquid and which from past of sub-division of ship shall be tested for tightness with water to a head up to the deepest sub-division load line
Or
To head corresponding to 2/3rd of depth from top of keel to margin line in way of tanks whichever is greater.
* Provided in no case shall the test head be less than o.9 meter above top of the tank.
Main Transmission Shaft
Electrical Cables
Fuel Oil Transfer Pipes